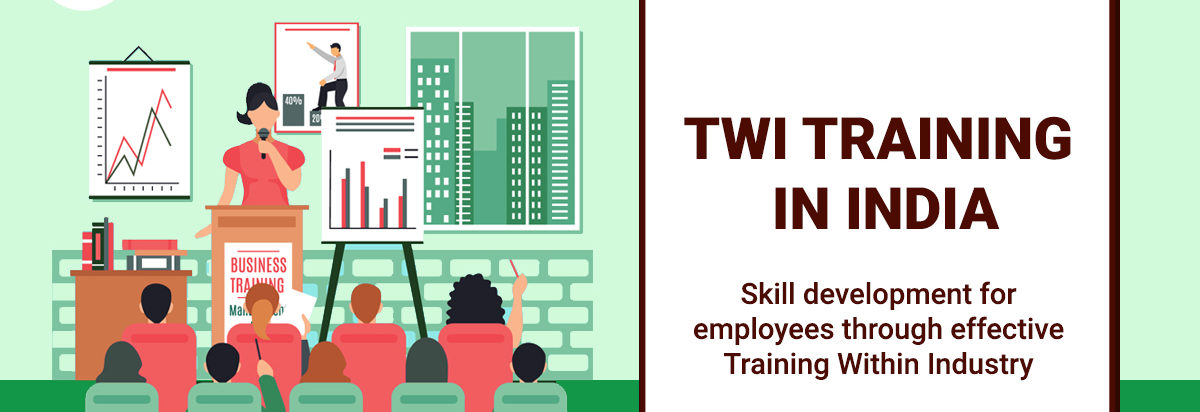
Skill development for employees through effective Training Within Industry – TWI training in India
More than 95% of the organisations give less importance for managing their human assets. This is no surprise if we come to know that nearly 100 years back, Henry Ford also commented which had a meaning that
“ why is it what when I want to hire a pair of hands- only physical labour, a brain comes attached (to people) ?”.
This concept has been highlighted through a fun movie Modern times where people are expected to do physical work and not contribute beyond that. Thinking, creating, improving and developing were activities were kept with very few – specific job profiles such as engineers, managers.
It is known fact that native born gifts of a person accounts to less than 10 % of the overall talent. 90 percent of the talent in the life of company employees is learned through own efforts, training and repeated practices. Self-learning is definitely an option but can take long time to learn. Success at best organisations can be traced to planned and effectively delivered talent development programmes. Companies like Toyota who believes in people development have invested dedicated training centres such as Toyota Technical Training Institute where they take competent and trainable people from various locations around their factories and with considerable time and efforts develop high levels of talent. It is hard to find ideal people who have exact skills that an organisation is looking for and that too in readymade form.
Many companies have a thinking that
“what if we train people and they leave us?”
For such people, there is also need to ask what if untrained people gets retained in the organisation and they will never want to leave? We end up with deadwoods.
Lack of training or ineffective training results in ineffective and suboptimal results. This results in too much firefighting which is not only time consuming but also results in loss of effectiveness and energies. This further leads to no time for training. This becomes a vicious cycle. We have to start with small investment of time in right training which inturn can give back multiple fold time to the organisation.
One of the Toyota’s principles mentions: Develop exceptional people and teams who follow your company’s Philosophy. Many organisations claim that they give importance of developing people within the organisations with a slogan on everywhere “People are our most valuable resources”. However, on ground the reality is people are ill-equipped to perform their basic jobs. There are no structured talent development plans and no skill matrix of operators too. We have seen many organisations who keep doing firefighting at senior management levels struggling to make on time dispatches/ order fulfilments even after having state-of the art manufacturing facilities and best in class machines. The missing link here is not having right skill of direct value adders – shop floor associates. Every company must have an effective method to train people. Rather than self-learning of key job roles which is very unorganized, the training courses should have direct reflection on key day to day jobs. This is where the so-called Human resources development members can facilitate the transition. Training job skills through On job training is one of the starting point to improve organisation performance. Job instruction method… one of the elements of Training within Industry will certainly be very useful for improving organisation performance.
Seven Steps Academy of excellence helps organisations through talent development through their flagship training programmes such as 5S training, Lean training, Lean Six Sigma Training – yellow belt, Green belt, Black Belt, Kanban training, Kaizen training, TWI training, TPM – Autonomous
Maintenance training, Kobetsu Kaizen training. Seven Steps Academy also trains young graduates out of college – mechanical engineering graduates in getting placements in precision engineering after intensive training and hands on skill development.
Seven Steps Academy is an associate company of Seven Steps Group. Our other division Seven Steps Business Transformation Systems helps organisations in their Journey of Excellence by deployment of various methodologies such as Lean thinking, Lean manufacturing Lean It, Lean services, TPM in process Industries, TPM in automotive industries. Our consultants are practitioners of such methodologies from various industries and we serve all over India, Srilanka, Dubai, Saudi Arabia. Our customers in India are located at Bangalore, Hosur, Chennai, Mysore, Visakhapatnam, Gurugram, Neemrana, Pant Nagar, Belgaum, Mumbai, Nashik, Calcutta, Jamshedpur, Coimbatore.
Seven Steps Business Transformation Systems is a Bangalore based consulting company for manufacturing, services, retail, logistics, construction, Education, hospital, hospitality. Kanban system implementation is done as a combination of other tools and methodogies such as 5S, Value Stream Mapping, Cellular Manufacturing, Total Productive Maintenance, Six Sigma etc., Through their group vertical – Seven Steps academy, various training programmes are also offered for both onsite and public programmes.
Some of the flagship training programmes conducted at Seven Steps Academy of Excellence are:
Six Sigma Yellow Belt
Skill development programme – Campus to Corporate – Precision Engineering
Lean Experimental Learning Programme