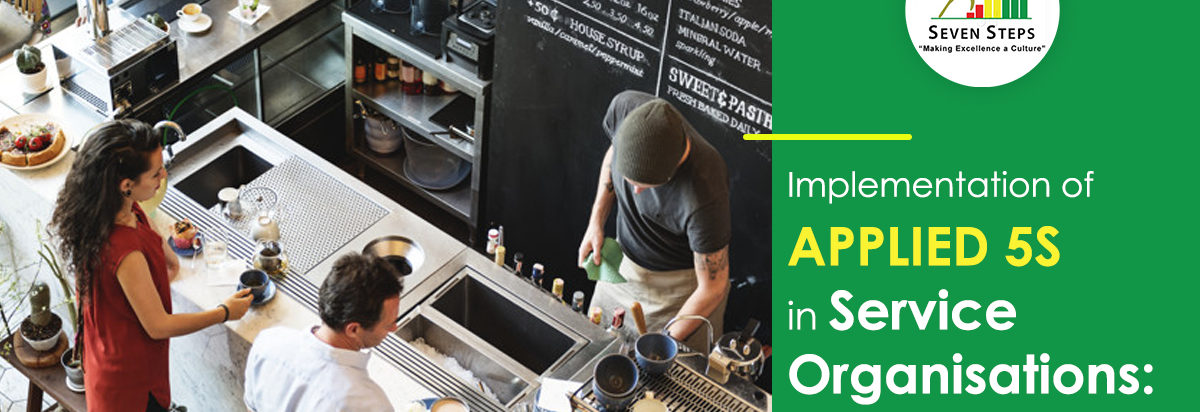
Implementation of Applied 5S in Service Organisations
Originated in America from ford (CANDO) -improvements) and strongly propagated by Henry Ford in his book – Today & tomorrow in 1926.
The excepts from his recommendations are as below:
- First thing to do every day is to clean up. Here it also means clearing up.
- Dirt is not affordable around the workplace as it is expensive.
- Expose abnormalities by having light background – white colour.
- Painting is not to cover up but to highlight.
“CANDO” is an acronym for
- Clearing
- Arranging,
- Neatness,
- Discipline
- Ongoing improvements
CANDO was translated into Japan by engineers from Japan Management Association – JMA which is Japan’s oldest and largest management training organisation. Major credit can be attributed to Takashi Osada who has served as a consultant on plant management, productive maintenance, Industrial Engineering, Quality Control, Process Control and small group activities. Takashi Osada has also helped in developing Total Productive Maintenance in Japan.
In the book The 5S’s, Five Keys to a Total Quality Environment,
the translation of CANDO is as follows:
- Seiri – as organization
- Seiton as neatness
- Seiso – as Cleaning
- Seiketsu as standardization
- Shisuke as discipline
These are not in exact sequence of CANDO. It was also called ONCSD with translated English words.
In simple words, 5s can be called a clean and well organized workplace. Does it apply for manufacturing only. Not at all, 5S can be applied to non-manufacturing areas such as offices, banks, retail outlets, supermarkets, Airports, Railway stations, Bus-stations, Metro Stations, Restaurants, Government, etc.,
Takashi Osada emphasized that without 5S, no other programmes such as TQC – Total Quality Control, Quality Circles, Kaizen, JIT, TPM can not succeed.
Related Article: Total Employee involvement through Quality circles and Kaizen Circles
A movement of 5S started as organisation wide and country levels. Similar programmes are in implementation in India from the government too such as Swatch Bharath. Unfortunately, the focus of Swatch Bharath has been similar to 5S which but not in the way it is perceived or implemented. Without structured implementation, 5S cannot be implemented or sustained.
5S looks easy to understand. However, they are very difficult to apply without a Guru or Coach or Consultant. Implementation of 5S required perseverance and determination and needs constant efforts to sustain.
Related Article: How to implement 5S and safety improvements in organisations
Many organisations claim to have implemented 5S some years ago. As per law of entropy, no condition remains in its state over a period of time. If the good condition of the factory or office is to be ensured, it has to be maintained in good condition with continuous effort.
Lack of 5S in such organisations will have the following scenarios:
- Loan applications cannot be traced and waiting for hours
- It takes a long time for security to give entry pass to important visitors
- Important forms will not be easily accessible
- Simple things like papers, staplers, pins are not easy to retrieve
- Customers are made to wait for long hours which results in frustration
- Essential items are not available for guests in a hotel
- Reservation process takes long time
- Waiting time in calls will be very high
- Order processing takes time
- Wrong product goes to customer
- Employees spend lot of time in searching for important things
- Employees productivity will be lower because of frustration.
- Lab reports take time to compile
- Inventory of value of items stored will be high: Many unwanted items will be available but not the one that are essential. It also results in expiry date items which eventually needs disposing and creating unwanted cost for operations.
- More space needed as unwanted items are occupying the place.
- Lack of teamwork.
- High absenteeism
- Safety hazards
Effective implementation of 5S helps in overcoming all the above scenarios. It also helps in togetherness and teamwork among the employees. Inspite of so many benefits of implementing 5S, why so many organisations are still working in old fashioned way with full of junks all over the workplace? The primary reason is that they are so difficult because they look so easy. Many people wants to work in their comfort zone and works in non-alignment with organisation’s’ objectives. They don’t understand that if one can’t do the 5S, they cannot do the other works which is so called important.
Related Article: Steps for Implementing the 5s Methodology
If a company is doing badly, it is most likely that its 5S is also very bad or it is not sustaining. 5S is also implemented as part of a back to basics initiative. To implement 5S correctly, right training is needed and the right way to implement and sustain is to be established. Taking external help is one proven way to establish a good foundation to last long.
Seven Steps Academy of Excellence offers training programmes as listed below:
- 5S
- Lean
- Lean Six Sigma
- Lean Six Sigma Green Belts
- lean Six Sigma Yellow Belt
- Lean Six Sigma Black belt
- 5s Auditor Training
- Kaizen training
- TPM Training
- Autonomous maintenance training
- SPC
- MSA
These programmes are offered as both public training programmes and inhouse training programmes in organisations.
Through our group vertical, Seven Steps Business Transformation Systems, implementation and hands-on support is provided for
- Lean manufacturing
- Lean in Hospitals
- Lean in Pharmaceuticals
- Lean Retail
- Lean logistics and supply Chain
- Value Added Management Systems
- Lean Six Sigma implementation
Seven Steps group is providing training and consultancy services in multiple sectors such as
- automotive
- pharmaceuticals
- construction
- hospitals
- education
- retail
- logistics
- supply chain
- aerospace
- defence
- oil mining
- continuous process plants etc
Related Article: Applying Lean methodology in Manufacturing, Retail, Logistics and Supply Chain management
Our customers are spread all over India ranging from locations such as
- Bangalore
- Chennai
- Mumbai
- Pune
- Calcutta
- Hosur
- Mysore
- Gurugram
- Chandigarh
- Ludhiana
- Neemrana
- Pant Nagar
- Visakhapatnam
- Salem
- Nashik
Our customers are also from
- Saudi Arabia
- Srilanka
- UAE
we cover other countries such as
- Africa
- Indonesia
- Japan
- China
- UK
- Germany
- USA
- Canada
- Singapore etc
Seven Steps Academy of Excellence provides training services in the field of Lean manufacturing, Lean Services, Lean Hospitality, Lean hospitals, Lean Supply Chain, Lean warehousing, Lean retain. As part of this, tools and methodologies for training includes Applied 5S, Lean Experiential Learning programmes, TPM Training, Six Sigma Green Belt and black belt training, Lean Six Sigma Yellow belt, green belt and black belt, Kanban supermarket. Apart from this, Campus to corporate programmes in precision engineering is also offered to aspiring engineering and diploma graduates through focussed skill development programme.
Through their group company – Seven Steps Business Transformation Systems, we also offer consulting services. We have consultants specialised in various methodologies and has worked as Lean consultants, Lean Six Sigma Consultants, TPM Consultants, 5S consultants, Lean layout consultants. We operate all over India and having branches in Bangalore, Chennai, Mysore, Hosur, Pune and have customer base in Delhi, Calcutta, Gurugram, Neemrana, Pant Nagar, Nashik, Pune, Hyderabad, Vishakapatnam, Vijayanagaram
Some of the flagship training programmes conducted at Seven Steps Academy of Excellence are:
Six Sigma Yellow Belt
Skill development programme – Campus to Corporate – Precision Engineering
Lean Experimental Learning Programme